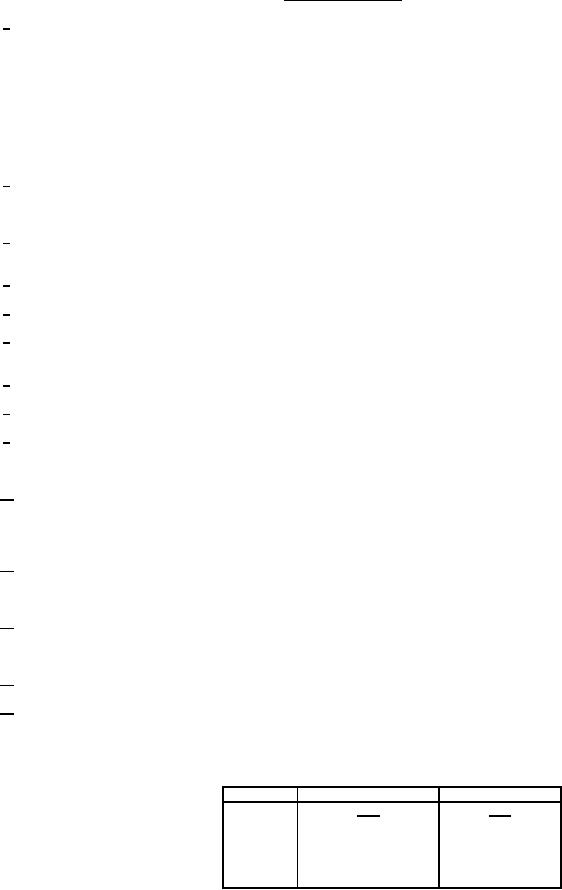
MIL-PRF-1/1037E
TABLE I. Testing and inspection - Continued.
1/
Torque test shall be performed as follows:
(a) The tube shall be held securely at the cathode connection. A force of 5 pounds shall be applied to the heater cup without
perceptible shock. This test may be made by applying the force at right angles to the inside of the cup at a point 0.109 inch (2.77
mm) H 0.016 inch (0.41 mm) from the cathode end of the tube. An approved equivalent method may be used. The heater cup shall
not loosen or short circuit on the cathode connection.
(b) A torque of 15 inch-pounds shall be applied between anode and cathode without shock.
(c) A torque of 40 inch-pounds shall be applied between anode and grid without shock.
2/
Test four tubes selected at random from the first production lot of each year. If more than one tube fails to pass the specified end
points, the failed test shall become a part of conformance inspection, part 2, with acceptance level of 6.5, inspection level S3, on all
lots in process. After three consecutive submissions, the test shall revert to a 4-tube annual test.
3/
Life test shall be run in cavity in accordance with Drawing 160-JAN (coupling: probe feedback and probe output) as a self-excited
oscillator.
4/
Life test shall be run in a self-excited oscillator cavity.
5/
Test in jig in accordance with Drawing 159-JAN.
6/
Other tube contact configurations may be used provided the tube contact area remains unchanged and the socket, jig, or cavity
gives equal performance. Mounting of the jig, socket, or cavity may be at the option of the manufacturer.
7/
The following does not apply: Tubes which show permanent or tap shorts or open circuits following the applicable test.
8/
All tests listed under conformance inspection, part 1, are to be performed at the conclusion of the holding period.
9/
Test to be made in cavity in accordance with Drawing 160-JAN. The cavity shall be connected to a standard load with a VSWR
less than 1.5. The output coupling from the oscillator and grid or cathode resistor, or both, may be adjusted for maximum power
output.
10/ Test 10 tubes selected at random from the first production lot of each calendar year and approximately every 90 days during the
year. If more than one tube fails to pass the specified end points, the failed test shall become a part of conformance inspection,
part 2, with acceptance level 6.5, inspection level S3, on all lots in process. After three consecutive successful submissions, the
test shall revert to a 10-tube quarterly test. This is a nondestructive test except in case of failure.
11/ Perform test on 10 tubes selected at random from the first production lot each calendar year. If more than one tube fails, the test
shall become a part of conformance inspection, part 2, with acceptance level 6.5, inspection level S3. After three consecutive
successful submissions, the test shall revert to an annual 10-tube test.
12/ Test to be conducted in power amplifier cavity. Driving power is defined as the net power delivered to the amplifier cavity input
terminals and the reflected power is to be subtracted from the incident power to obtain the net driving power. The output tuning and
load coupling are to be adjusted for maximum power output.
13/ Measured in socket in accordance with Drawing 158-JAN.
14/ Grid - anode resonance:
Test in cavity in accordance with Drawing 278-JAN. Cavity shall resonate at 1.354 GHz
H 2.0 MHz with tuning slug in accordance with Drawing 277-JAN at TA = 25G H 5GC.
When plotted on graphs of resonant frequency versus grid-anode capacitance, the tube under test shall be represented by a point
within a parallelogram whose four corners are located by the following points:
Points
Capacitance (pF)
Frequency (GHz)
Cgp
Fgp
1
1.89
1.92
2
1.89
1.95
3
2.13
1.87
4
2.13
1.90
5
For Parts Inquires call Parts Hangar, Inc (727) 493-0744
© Copyright 2015 Integrated Publishing, Inc.
A Service Disabled Veteran Owned Small Business